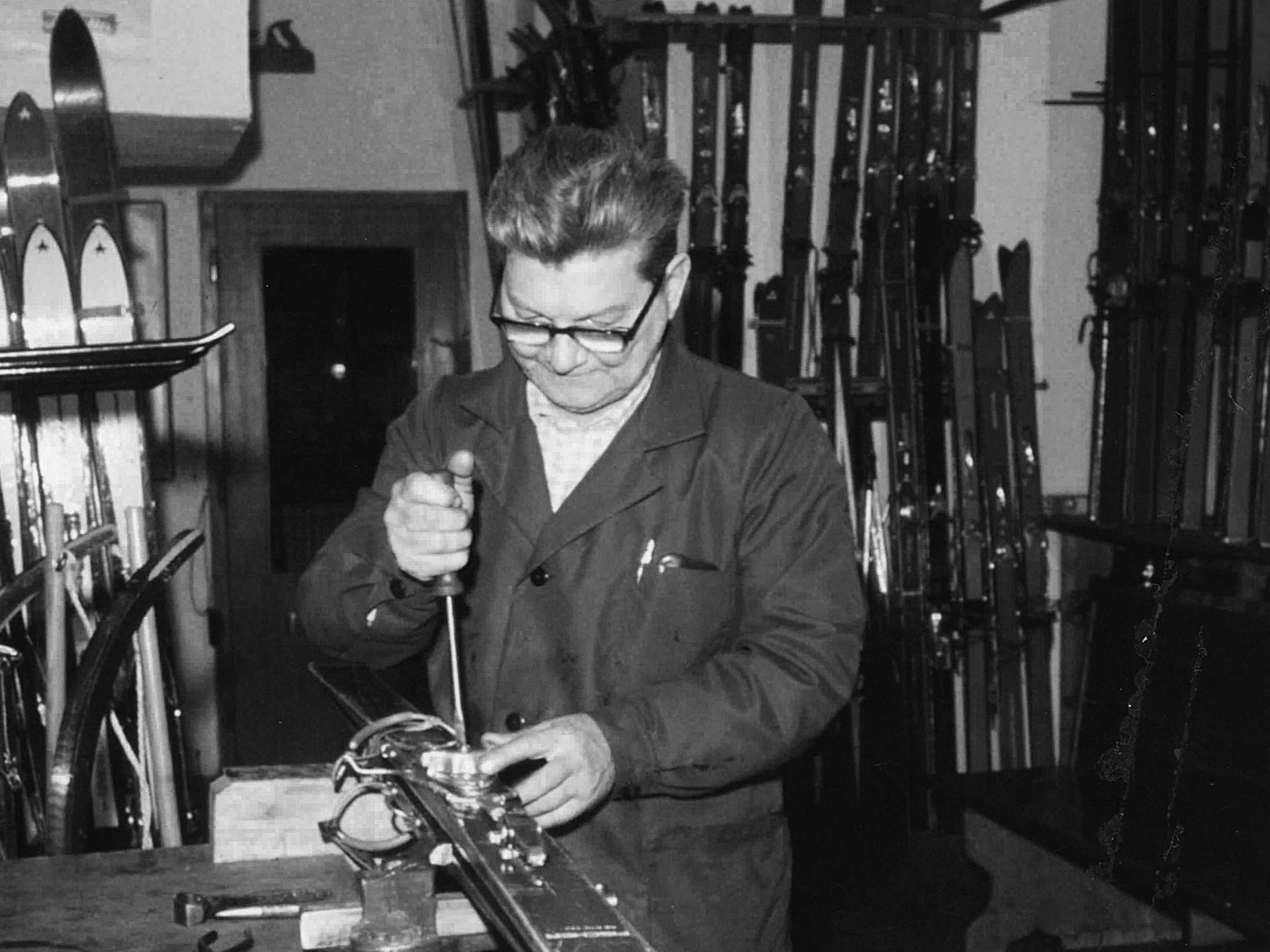
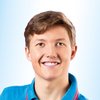
How a simple curved ash board became high-tech sports equipment.
Paul Pangratz, CEO
How a simple curved ash board became high-tech sports equipment.
Paul Pangratz, CEO
Arlberg Magazine, #1 – Winter 2013/14.
In a time where many horse-drawn wagons needed repairs, a few innovative people were thinking about winter sports. In the 1920s Hermann and his wife Pia recognized the potential for business as groups of winter English tourists were in town; hence the first sports store was opened in St. Anton.
As early as 1926 Pangratz started his own ski production under the brand name “Pangratz”. Ski production back in the 1920s is nothing like it is today. The skis were mainly made from local Ashwood and largely made by hand over the summer, so that they were ready for rent or sale to visiting winter guests. The bending of the ski tips was achieved by means of steam and a martial press. Edges and safety bindings were not even a concept back then.
It was only after the war years, that the production of skis in Haus Pangratz began with the first bolted-on edge. “The hardest work that exists”, Toni Pangratz, Patrick’s father, would famously report. Also, during his time he had a decision to make whether or not he should buy a piece of land that was for sale in Nasserein or buy a circular saw that would enhance ski production. Both transactions required a large financial expenditure. The decision was made for circular saw. A pure entrepreneurial spirit indeed, compare today’s land prices with those of a circular saw.Toni Pangratz in 1960 after completing his sales training education at trade school appointed a wagon repairman apprentice in his father’s Hermann’s repair shop and commenced producing the much beloved Pangratz skis for another decade.
Until the late 1960’s, more than 100 pairs of skis were made in a 70m2 workshop with the help of employees. The vast majority of them were made available in their very own on-site ski rental shop, which at the time impressively was well equipped with over 1,000 pairs of skis and was the first in St. Anton. When the major leading ski manufacturers, like the Family Kneissl, with St. Anton’s very own Karl Schranz as their brand champion, revolutionized the manufacturing of factory made skis in large quantities, the days of handmade regional ski makers like Pangratz were numbered. Not just the processed materials – starting with the layered glue wood, then later fibreglass, were becoming more efficient but so was production which forced them to capitulation. Toni Pangratz and his wife Irene recognized the signs of the times and concentrated from then on, on their sports shop that was founded in the 1930s and was built on their core competence and the following year expanded their rental services.
To this day, the shop remains faithful to their business model by taking the next step ensuring even more solid foundation by joining forces with the Ess family as Intersport Arlberg in 2000. There are a few preserved tokens of ski production that can still be admired exhibited in the lobby of Pangratz’s Life and Style hotel “Anthony’s”.
How ski production is today, the management crew of Intersport Arlberg got an idea of how it’s done this past end of September by visiting the Atomic factory, owned by Amer Sports, in Altenmarkt, Austria. There you remember nothing of the old times, although even today many work stages are still done manually. Finally ski production in the 21st century is very high-tech and in many areas an automated process. This is proven by the countless models available for racers, free riders and all-around skiers. Although in-house ski production is a thing of the past, INTERSPORT Arlberg employees are always close to the action and with the employee development program 2020 are kept up-to-date. The ultimate goal is to understand client’s requests and to fulfil their needs whenever possible.